Designing Durable Furniture and Equipment with Acrylic Solid Surface
In our latest blog post, we introduced a recent publication from the American Society of Health Care Engineering (ASHE) titled Using the Health Care Physical Environment to Prevent and Control Infection. The result of the collaborative research initiative is an evidence-based best practice guide to help health care organizations create safe, healing environments. As it relates to furniture, the guide introduces design recommendations with a simple goal—help provide easier means of cleaning for better outcomes.
The five furniture surface characteristic recommendations outlined on page 107 are: durability, cleanability, inability to support microbial growth, surface porosity, and absence of seams. Although acrylic solid surface is capable of complying with all of those evidence-based recommendations, today’s article will focus on the first, durability, explaining what the material is and how it’s being used to support better design in health care.
"Solid Surface"
Today, many manufacturers make raw acrylic solid surface sheet goods. DuPont’s Corian® is the original acrylic solid surface. Now that the patent has expired, other brands have established themselves in the market with similar products, such as LG’s Hi-Macs® and Lotte Advanced Materials’ Staron®. The primary differentiator between the brands are largely aesthetic, but collectively they offer designers an unlimited design palette with unparalleled durability.
Although designers and manufacturers use the term “solid surface” loosely to describe manufactured sheet goods (even at times referring to silica-based stone and quartz materials), there are two types of solid surface in particular with very distinct differences - polyester solid surface and acrylic solid surface. Shield builds healthcare products using acrylic solid surface because it’s stronger, easier to seam, and better suited for thermoforming. When completed to a matte finish, it’s also easier to clean and maintain over the life of our products.
Acrylic Solid Surface Composition
Not to be confused with polyester solid surface, the composition and performance qualities of acrylic solid surface can provide significant short and long-term benefits when compared to wood, plastic laminate, metal or stainless steel in furniture and equipment. We've covered the composition and benefits of acrylic solid surface in a previous blog post, but let’s review those briefly.
The primary ingredient is derived from a naturally occurring mineral and is called Aluminum Trihydrate (ATH), which accounts for roughly 60% of the material. This non-silica based ingredient is likened to stone dust, but it’s non-toxic and adds tensile strength to the final product. It’s also flame-retardant, and largely responsible for giving acrylic solid surface it’s class A fire rating.
The second ingredient is the bonder, polymethyl methacrylate (PMMA), which is commonly known as acrylic. This is the binder that, once cured, preserves the shape and allows the material to be loaded. It’s what makes solid surface non-porous. PMMA also allows the material to be super heated and thermo-molded into complex shapes, returning to it’s original, durable state once cooled.
Each sheet can be anywhere from 90-99% ATH and PMMA depending on the color and finish selected. Once combined and cured, the final product is homogenous and inert. In fact, acrylic solid surface is also GREENGUARD certified for building products and interior finishes. It also carries healthcare product declarations (HPD) and environmental products declarations (EPD) from most manufacturers.
Fabricating with Acrylic Solid Surface
One of the primary challenges of building with acrylic solid surface is connecting to it. Unlike wood-derived or metal materials, you can’t screw directly into the material, which is why most manufacturers that work with acrylic solid surface either clad it to a substrate using adhesives, or they’re required to “double-up” the material, creating a through-connection that fixes to a secondary, load-bearing substrate. Simply, acrylic solid surface has historically been used as a high-quality laminate.
Traditional methods of building products with solid surface are flawed, and here’s why. In the former method, the final product only presents the appearance of an acrylic solid surface product that in reality is only clad with the material. The latter method doubles the amount of material used, which contributes to additional and unnecessary cost and weight to the final product.
In order to fully leverage the durability of acrylic solid surface in final products, Shield developed a patented system of building with and connecting to half-inch acrylic solid surface unlike any other manufacturer. In particular, Shield discovered that their embedded stainless steel insert technology gave them two advantages: it allowed them to build structurally with acrylic surface, which eliminates the need to use less durable substrates and reduces material cost; and it created remarkably strong connections for hardware, which have been tested to failure at over 700 pounds of pull out strength, per screw. Shield has also developed proprietary joinery techniques that increase the strength of the product while reducing fabrication time.
Shield has invented new ways of building with the material to largely eliminate the need for substrates. These manufacturing techniques allow Shield to fabricate products made almost entirely from acrylic solid surface. When combined with digital fabrication techniques and thermomolding capabilities, your design visions come to life without compromising the durability, cleanability, or even our warranty of the product. No other manufacturer has matched our industry-exclusive limited lifetime warranty - talk about durability.
Acrylic Solid Surface in Healthcare
Acrylic solid surface is already a design standard for countertops in healthcare because it’s durable, easy to maintain and renewable. Acrylic solid surface is resistant to scratching and chipping and holds up to medical disinfectants, as recommended by the best practice guide.
Furthermore, the material is homogenous, which means it’s the same material end to end. The material remains easy to clean or disinfect through normal wear and tear and doesn’t promote the growth of microorganisms. In fact, normal wear and tear is easily repairable by facilities maintenance staff using a damp Scotch-Brite pad, which allows Shield to offer a low-maintenance, lifetime product guarantee.
Shield works collaboratively with designers and multi-disciplinary teams to develop products for healthcare, which aligns with the secondary goal of the best practice guide. In practice, Shield’s products are typically born out of necessity, stemming from either continued failure of traditional products using traditional materials, or the need for products to function better using smarter materials than what the market currently offers.
Shield's operating room documentation stations are the result of a design collaboration with the University of Kansas health system and Cannon Design. The creation story of our documentation stations gets to the heart of why we do what we do. We hope it inspires you to share your design challenges with us.
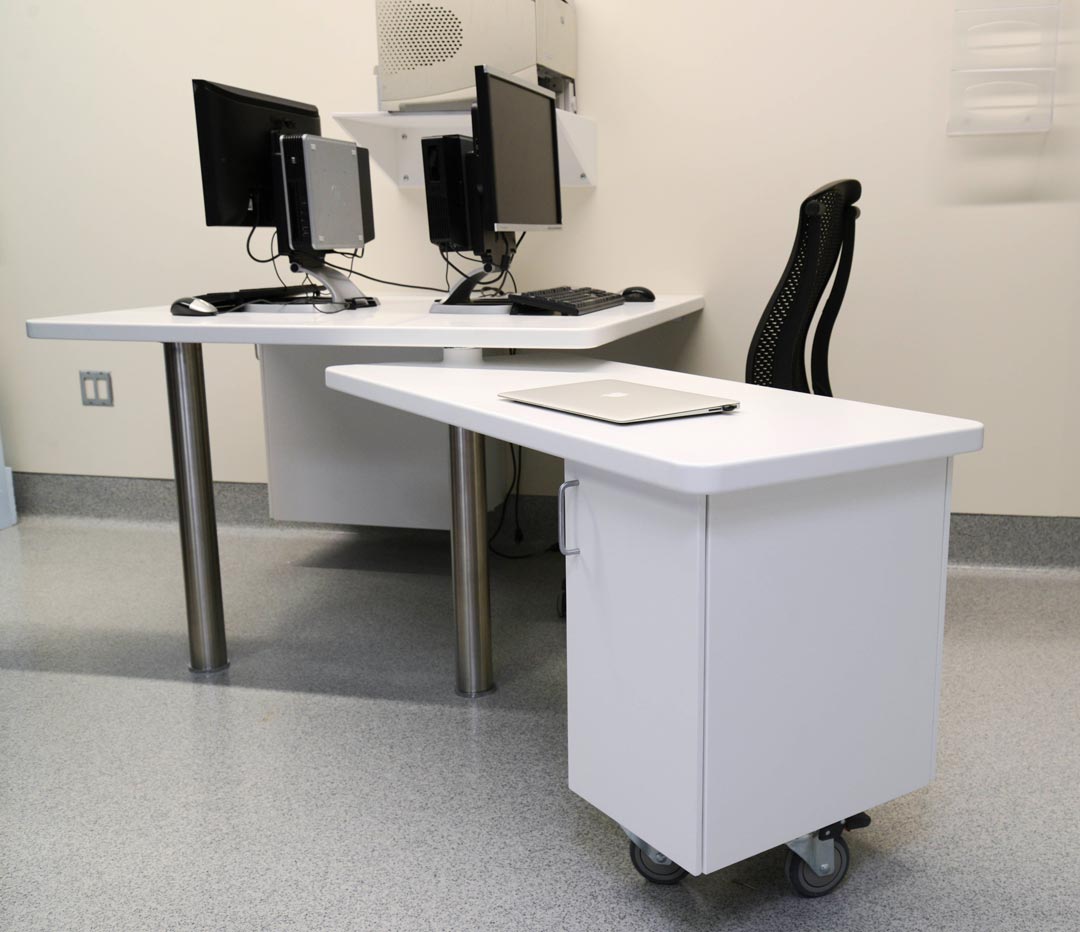
Do you have a design project that you think would be well-suited for acrylic solid surface?
Contact Shield to learn more about our custom design services or visit our products page for more information.